Case Study: ESG and Energy Consumption
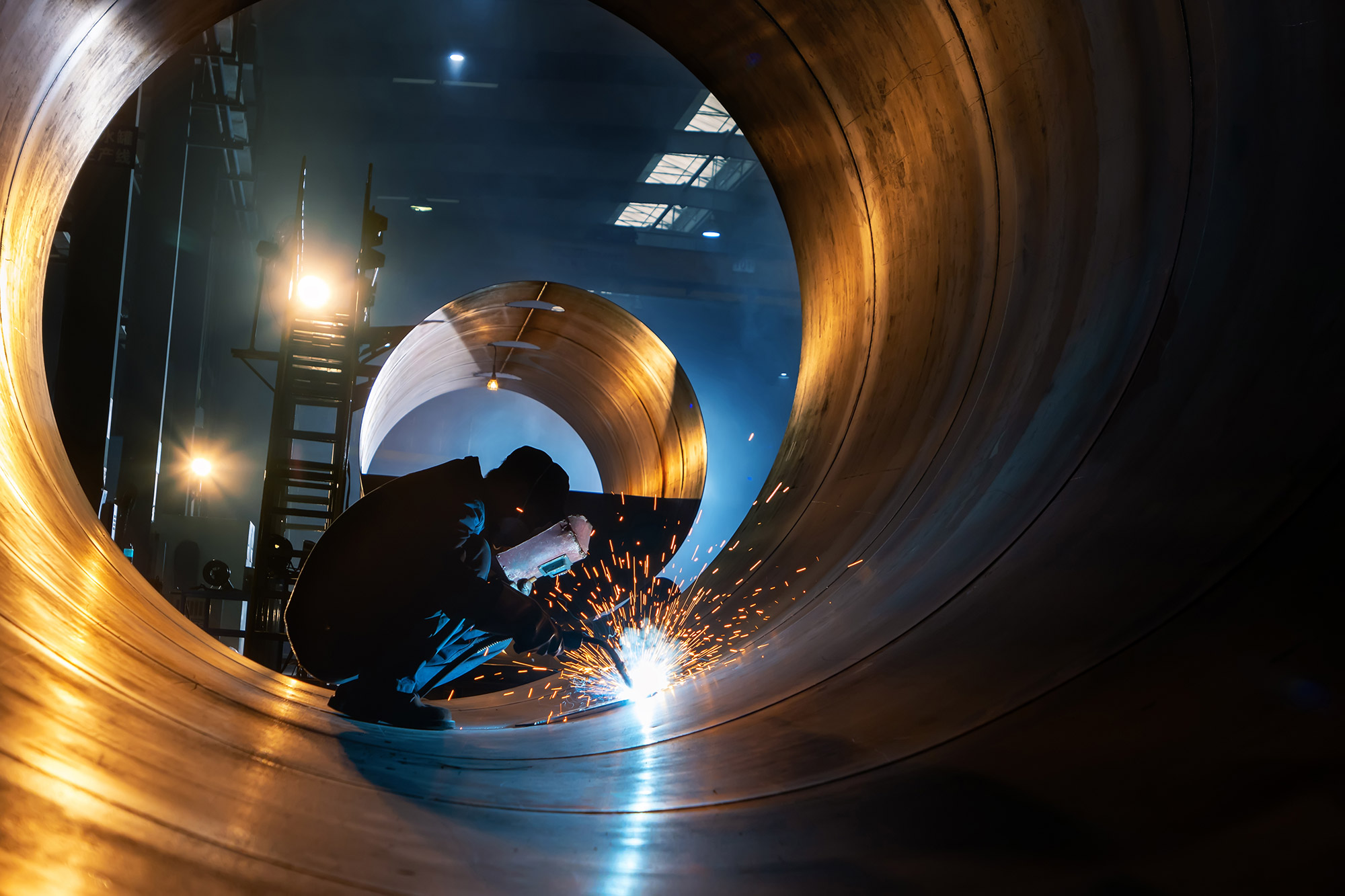
Discover how our Industrial Data Collection transformed a manufacturing giant by monitoring energy usage, saving costs, and boosting efficiency across a sprawling facility. Real-time insights for impactful change.
The Challenge:A leading manufacturer of large metal infrastructure faced the challenge of optimizing energy consumption within a sprawling 50,000 square meters manufacturing facility. With rising operational costs and an emphasis on sustainability, the company sought a solution to monitor energy usage, identify inefficiencies, and implement targeted improvements.
A significant portion of the overall energy consumption can be traced to 130 power-hungry welding stations that were prone to being left turned on by distracted employees and expensive and unautomated HAVC systems running unnecessarily off-hours. Although the stations didn’t consume much energy when left on, there was still an unnecessary waste of electricity.
The Solution:
Our Industrial Data Collection turnkey application—a tailored solution that seamlessly integrated into the manufacturing environment.
A robust local data collection mesh network was deployed across the facility, covering every corner. Over 100 cost-effective power consumption sensors, ranging from 32A to 500A CTs, were strategically installed to monitor the current leading to the welding stations.
The solution was a self-contained and secure system that offered real-time energy consumption monitoring, facilitating proactive insights. The solution allowed shift managers to identify in real-time which stations were left on unnecessarily, leading to better oversight and improved practices aimed at promoting efficiency and accountability.
The Results:
The implementation of the Industrial Data Collection application yielded substantial benefits:
- Cost Savings: The company achieved a significant reduction in costs. Over a period of 48 months, typical electricity consumption expenses totals €8,800,000. Real-time monitoring led to 10% energy savings, equivalent to €880,000. This achievement translates into a compelling return on investment, realized within just 6 months.
- Efficiency Enhancements: The real-time monitoring capability had a direct impact on operational efficiency. The system ensured that all welding stations were powered off at the end of each shift. In case of accidental oversight, designated managers received immediate alerts. This actionable insight enabled the company to implement targeted measures for energy efficiency and consumption reduction.
- Total Benefit: The cumulative benefits are substantial. Over the 48-month period, the company reaps total benefits amounting to €790,000. This comprehensive achievement underscores the value of real-time monitoring and data-driven decision-making.
In essence, the implementation of the Industrial Data Collection application revolutionized energy management for the manufacturer. The marriage of wireless technology, real-time monitoring, and data analytics translated into tangible financial gains, swift ROI, and a robust foundation for ongoing efficiency enhancements.